How Critical is System Visibility in Warehouse Automation?
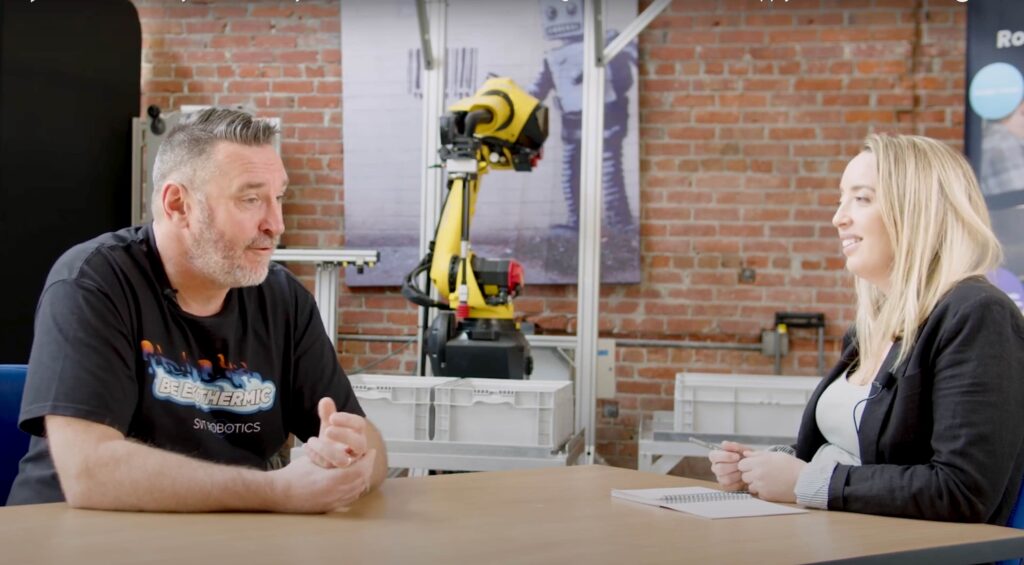
In this episode, Steve Thorne, VP of Product Success at SVT Robotics shares lessons learned from his 24 years in supply chain deployment and specifically dives into the importance of system visibility when it comes to your automation integration.
Chloë: Thank you for joining us. So, we want to help those who are starting their automation journey, whether in the initial stages of scoping out a project or further along, to learn from your experiences in the industry.
Steve: Sure. I landed in this industry by accident. My background was in electronics, and I started doing software in the late ’90s. I found a job in software because, back then, software engineers were in high demand due to the dot-com bubble. In fact, I was the only one who showed up for an interview, despite knowing nothing about warehousing or relational databases. I spent the first year thinking, “They’ll find out I know nothing.” But that’s how I got into the industry, working in software engineering and gradually shifting to solution architecture.
Chloë: How have you found working in this industry?
Steve: My favorite part is seeing things move, especially the tangible and rapid results. Whether it’s software or a project, it’s satisfying to watch complex systems function. Even seeing something like a labeled box in a grocery store and realizing I contributed to that process is very rewarding.
Chloë: You were a systems integrator. What problems did customers bring to you to solve?
Steve: Initially, it was about optimizing warehouse storage. Over time, it shifted to system integration and finding ways to streamline processes, considering factors like temperature control for products moving through warehouses.
Chloë: What made deploying automation challenging?
Steve: Integrators often had their equipment line, but customers often required unique technologies or specific types of robots. Getting different technologies to communicate was a struggle. There was friction due to resistance in changing systems and adapting technologies to work together.
Chloë: Can you describe a time when these challenges affected a project?
Steve: I remember a pharmaceutical project in Holland where a system failure halted everything. It took hours to find the problem, and executives were watching. The issue was an incomplete transmission of a crucial message, and the system was down for hours. It was a tense situation, trying to resolve the problem. I was even forced to flip a coin to decide on the solution, and it worked. I was lucky. And the whole situation underscores just how critical system visibility is to these solutions.
Chloë: What makes integration difficult?
Steve: Every technology has its unique way of communicating and interpreting data, making translation and coordination complex. There’s often a lack of common understanding among different tech systems.
Chloë: How does the SOFTBOT Platform help address these issues?
Steve: SOFTBOT acts as a universal mediator between technologies. Any system only needs to integrate with the SOFTBOT Platform, making multi-tech communication much more straightforward. It reduces custom coding needs and enables faster deployment, even in instances like system upgrades or transitions.
Chloë: And what about the prebuilt integrations and orchestrations?
Steve: Connectors are prebuilt to work with specific use cases like orders. Orchestrations ensure these connectors transform data to fit each technology’s requirements, enabling smooth communication among different systems.
Chloë: Sounds like a pivotal solution in a complex environment. What do you foresee in the future of warehouse automation?
Steve: I see a future where systems are more interconnected, reducing the barrier between different technologies. The goal is to reach a stage where system integration feels more like linking Lego blocks rather than intricate, complex coding and troubleshooting.
Chloë: Fascinating. Thank you, Steve, for sharing your insights and experiences in the field.
This interview has been edited for length and clarity. Please listen or watch the episode to catch the entire conversation.