Lessons from Deploying $500M in Supply Chain Automation
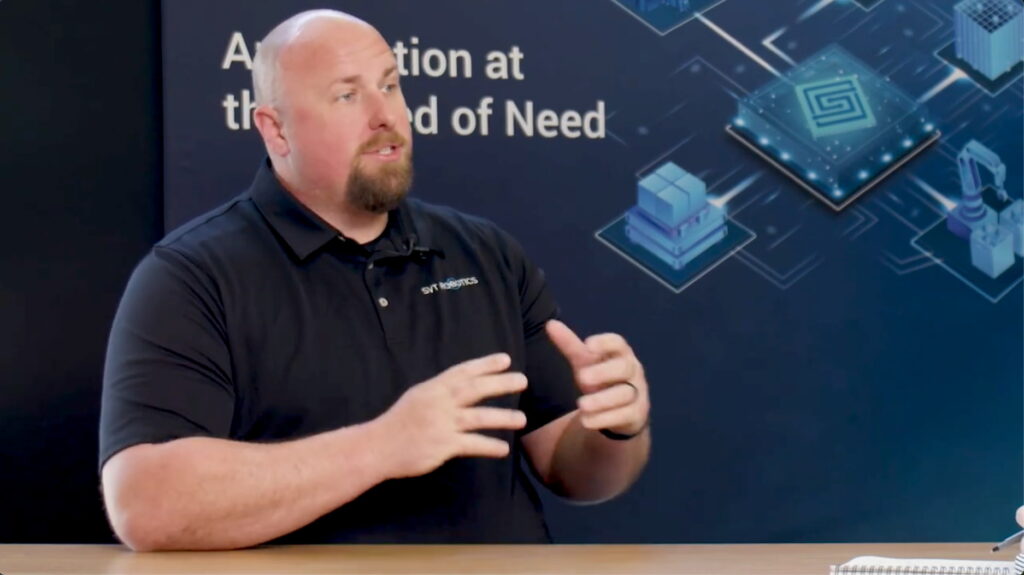
Chloë: Welcome, everyone! I’m joined by Nick Leonard, SVP of Product at SVT Robotics. Today, we’ll discuss his insights from deploying over 500 million in automation solutions in supply chain. That’s a big number.
Nick: Absolutely. Yeah, it struck me when I began totaling all the deployments I’ve been part of in my career. Just adding it up.
Nick: Surprising, for sure. It sneaks up on you.
Chloë: It’s probably not that hard, considering every project is quite a chunk of change.
Nick: Definitely. Initially, in my career, I was dealing with larger-scale deployments. A couple million each time, sometimes tens or even a hundred million dollars a year.
Nick: It’s easy for those numbers to add up, but it’s an interesting thing to think about.
Chloë: So, that leads to my first question. How did you start in this industry?
Nick: I never planned to be in warehousing logistics. It sort of happened after college. With an information science degree, I was exploring roles that applied software to real-world problems. I found a job posting for a junior IT project manager in a large logistics company and jumped in. That’s how my journey in project management began, focusing on applying software controls to automation.
Nick: I fell in love with that challenge and stayed with it since.
Chloë: Interesting. So, you spent a significant time at a systems integrator. What kind of issues did customers bring to you for solutions?
Nick: Often, they were aiming at labor reduction but with the aim to increase facility capacity within their existing network. They needed to enhance storage density, input/output, and throughput without relocating their entire operational staff. We aimed to extend or enhance their facility capabilities.
Nick: Then it was about process optimization, using software to integrate their automation journey.
Chloë: Could you talk about challenges faced while scoping new solutions and piecing together different systems?
Nick: Often, the immediate need for automation is understood, like the need for faster picking or better storage density. The operational challenges are clear. But the tricky part is understanding how to translate those needs into automation, especially for those new to it.
Nick: It usually starts with a data study to understand the facility’s actual throughput, orders fulfilled, dock speed, storage density, etc., beyond traditional operational analysis. This data can reveal new insights, sometimes shifting the problem statement itself.
Nick: Selecting the right process to automate is often challenging. Most would want to automate the most laborious tasks, but it’s better to start with simpler movements in the warehouse.
Chloë: Once you’ve scoped out a solution, what’s the next step in the process?
Nick: It’s about translating how automation integrates into the existing facility’s material movement. This might require operational changes. Automation isn’t standalone; it needs data for intelligent decisions. So, the software is critical. Bringing in a warehouse execution system, integrating with WMS, and addressing business logic are vital. These systems are no longer simple; they need fundamental understanding.
Chloë: Could you share examples of projects where reconciling different data models and components proved particularly challenging?
Nick: Simple projects like transporting automation are straightforward, but when you aim for multi-operational interoperability, it gets complex. Connecting various systems and hardware, while ensuring flexibility, becomes essential, especially for large-scale integrations.
Nick: The challenge lies in integrating inflexible hardware and adapting it to new requirements. System changes can have ripple effects, impacting different steps in the process. Building automation at scale involves intensive data study and analysis.
Chloë: Fascinating. Now, can you highlight reasons for the failure or lesser success of automation projects?
Nick: Selecting the wrong operation to automate is a common problem. Complexity in automation projects can reduce their intended ROI. Inaccurate or manually taken data can significantly affect the success of larger operations. The wrong technology selection can also derail the project.
Nick: Lastly, inadequate IT involvement, incorrect or incompatible system integrations, and poor data sharing between systems all contribute to the failure or inefficiency of an automation project.
Chloë: In the supply chain industry, connecting different technologies often proves difficult. Can you elaborate on the challenges in this space?
Nick: Infrastructure is the primary challenge. Many warehouses still run on paper or Excel, and upgrading to automation can overwhelm the existing infrastructure. Connecting different systems often requires adaptations due to differing APIs and data tags. Mapping this data from one system to another can take weeks of effort.
Chloë: And when new technology or business requirements come in after the initial deployment, how does that impact the existing setup?
Nick: Addressing changes post-deployment can be complex. Customizing technology and systems after integration can be time-consuming and costly. Retooling the system post-deployment for new requirements often triggers negotiations, impacts timelines, and requires rethinking system logic and flow.
Chloë: With all this insight, what advice would you offer those embarking on their supply chain automation journey?
Nick: Start with the data, digitize operations, and start with a small, proven project with a discreet ROI. Plan for iterations and learning. Being ready to evolve is critical because automation, like businesses, needs to adapt to change.
Chloë: That’s incredibly insightful. Thank you so much, Nick.
Nick: Absolutely, Chloe. Cheers.