How 10 Minutes Of Manufacturing Downtime Nearly Crippled A Chocolate Company
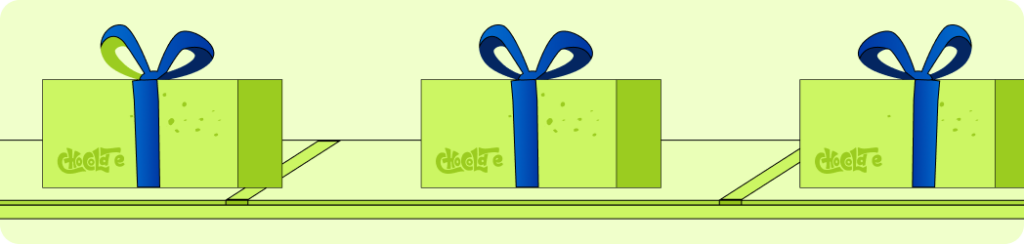
Manufacturing downtime can prove fatal for many companies worldwide. In the fast-paced manufacturing world, time is more than just money—it’s the lifeline that either keeps businesses thriving or sends them spiraling into chaos. Nowhere is this truth more apparent than in the cautionary tale of a European chocolate manufacturer that found itself on the brink of disaster, all because of a mere 10-minute delay.
This cautionary tale, shared by industry veteran Jay Blinderman, our SVP of Go-to-Market at SVT Robotics, starkly reminds us of the critical importance of uptime in modern manufacturing and highlights how innovative solutions like SVT Robotics’ SOFTBOT® Platform can be the key to averting such crises.
The 10-Minute Meltdown: A Closer Look
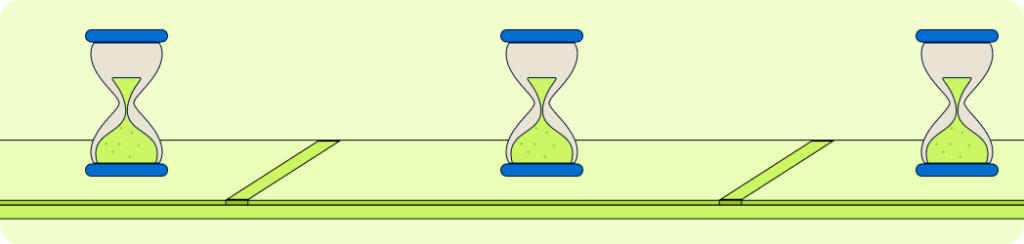
Picture this: A state-of-the-art chocolate manufacturing facility operating with the precision of a well-oiled machine. At the heart of this efficient operation is an enterprise software system orchestrating every aspect of production, from the initial mixing of ingredients to the final packaging and distribution.
But what happens when this well-oiled machine grinds to a halt? Years ago, Blinderman had to deal with this issue head-on. The chocolate company’s system had a critical vulnerability: if any manufacturing line remained stagnant for more than 10 minutes, it triggered a cascade of consequences that would keep any business owner up at night.
The Domino Effect of Manufacturing Downtime: A Detailed Breakdown
- Wasted Product: All chocolate on the lines had to be discarded. In a large-scale operation, this could mean thousands of pounds of premium chocolate—ranging from liquid chocolate in tempering machines to partially formed confections on cooling belts—all destined for the waste bin.
- Sanitation Overhaul: The entire production line required sanitization. This isn’t a simple wipe-down; it involves meticulously cleaning every surface that came into contact with the now-wasted chocolate. Mixers, molds, conveyor belts, and packaging machinery must be thoroughly cleaned and sanitized to meet strict food safety regulations.
- Production Halt: Operations ground to a stop for over an hour. During this time, not a single chocolate bar or truffle was produced, creating a significant gap in the day’s production quota.
- Missed Deadlines: Customer deliveries were delayed. In the just-in-time inventory world of modern retail, these delays can have far-reaching consequences. Imagine empty supermarket shelves or a Valentine’s Day promotion falling flat due to missing stock.
- Financial Penalties: Late deliveries to major clients like Walmart incurred hefty fines. Large retailers often have strict policies about delivery times, with financial penalties for missed windows. These fines can quickly eat into profit margins.
- Labor Costs: Overtime and additional shifts were needed to catch up. Workers who were scheduled to end their day might now be asked to stay late, incurring overtime pay. Extra shifts might sometimes be necessary to compensate for lost production time.
- Employee Burnout: Workers faced increased stress and longer hours. The pressure to make up for lost time can lead to fatigue, potentially increasing the risk of errors or accidents.
The total cost? A staggering $100,000 or more per incident. And that’s just the immediate and quantifiable impact!
Beyond the Balance Sheet: The Hidden Costs of Manufacturing Downtime
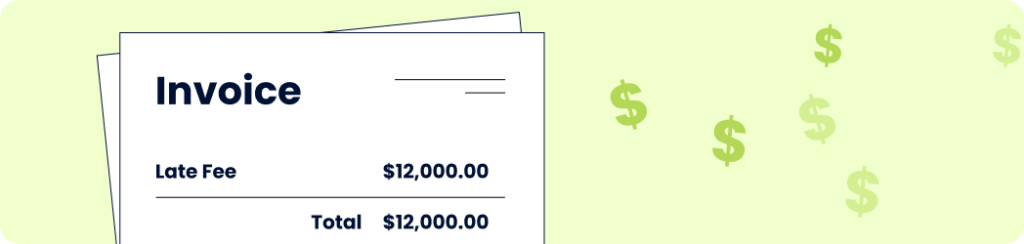
While the immediate financial impact is shocking, the long-term consequences of such incidents can be even more severe:
- Customer Dissatisfaction: Repeated delays erode trust and may lead to lost contracts. In a competitive market, customers have alternatives. Buyers might switch to more dependable suppliers if a chocolate company can’t deliver reliably.
- Market Reputation: In the age of social media, news of manufacturing downtime spreads quickly. A single tweet about empty store shelves or a missed holiday delivery can spiral into a PR nightmare, affecting brand perception and future sales.
- Inventory Inefficiencies: To combat downtime, companies often overstock, tying up capital and reducing overall efficiency. This “just-in-case” inventory strategy leads to increased storage costs, potential waste of perishable ingredients, and reduced flexibility in responding to market demands.
- Employee Morale: Constant firefighting leads to stress and decreased job satisfaction. When workers feel like they’re always in crisis mode, it can lead to burnout, higher turnover rates, and difficulty attracting top talent.
- Innovation Stagnation: When resources are constantly devoted to fixing problems, there’s little time or budget left for innovation. This can leave companies vulnerable to more agile competitors who can introduce new products or improve processes.
- Regulatory Risks: In the food industry, consistent production issues can attract unwanted attention from regulatory bodies. Increased scrutiny can lead to more frequent inspections, potential fines, or even forced shutdowns.
Jay explains: “There’s impact to their margins, their bottom line, customer satisfaction, labor issues, and more. There’s a lot of impact on downtime that goes well beyond IT’s control.”
The Ripple Effect: How Manufacturing Downtime Impacts the Entire Supply Chain
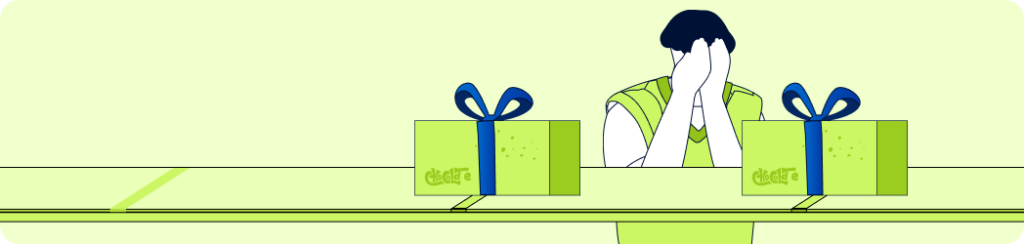
The consequences of downtime extend far beyond the walls of the chocolate factory. Let’s explore how a 10-minute delay can create a ripple effect throughout the entire supply chain:
- Supplier Relationships: When production unexpectedly stops, scheduled deliveries of raw materials like cocoa beans, sugar, and milk powder may need to be postponed or canceled. This can strain relationships with suppliers and potentially lead to less favorable terms in the future.
- Transportation Logistics: Trucking companies and shipping partners rely on precise schedules. When products aren’t ready for pickup at the agreed-upon time, it can throw off entire routing schedules, leading to additional costs and inefficiencies.
- Retail Partners: Beyond the fines for late deliveries, retail partners may face their own set of consequences. Empty shelves can lead to lost sales, disappointed customers, and a damaged retailer’s reputation.
- Consumer Trust: In today’s connected world, consumers are increasingly aware of and interested in the source of their products. Consistent supply issues can erode trust not just in the brand but in the entire supply chain, leading consumers to seek out alternatives they perceive as more reliable.
- Economic Impact: For regions where chocolate manufacturing is a significant industry, repeated production issues can have broader economic implications, affecting local employment rates and regional economic stability.
Streamlining Success With The SOFTBOT Platform
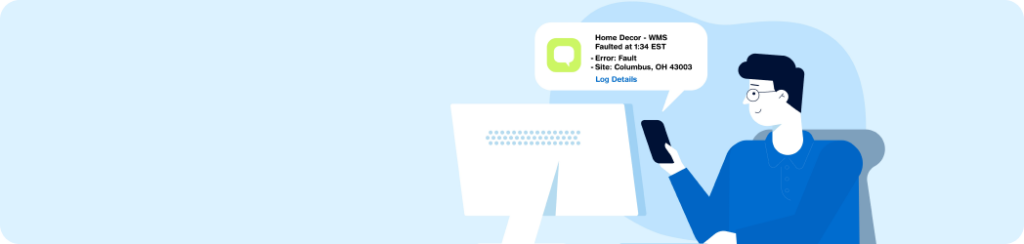
Imagine transforming that 10-minute crisis into a minor blip on the radar. With SVT Robotics’ SOFTBOT Platform, manufacturers can:
- Minimize downtime and associated costs, protecting profit margins and maintaining production schedules
- Improve customer satisfaction through reliable deliveries, building stronger, more trusting relationships with retailers and end consumers
- Optimize inventory management, reducing waste and improving cash flow
- Enhance employee satisfaction by reducing stress and overtime, leading to a more stable and skilled workforce
- Maintain a competitive edge in a fast-paced market by focusing on innovation rather than constant troubleshooting
- Ensure regulatory compliance by maintaining consistent, documentable production standards
Embracing the Future of Manufacturing
In today’s rapidly evolving manufacturing landscape, the ability to adapt quickly and avoid manufacturing downtime is more than just a competitive advantage—it’s a necessity for survival. The story of the chocolate company serves as both a warning and an inspiration. It shows us the potentially devastating consequences of even minor disruptions but also highlights the transformative power of innovative solutions like SVT Robotics’ SOFTBOT Platform.
As we move further into the age of Industry 4.0, with its emphasis on interconnectivity, automation, and real-time data, offerings like the SOFTBOT Platform will become increasingly crucial. They represent a safeguard against disaster and a pathway to new efficiency, quality, and innovation levels.
Don’t let your business become the next manufacturing downtime horror story! Embrace the power of intelligent automation with SVT Robotics and keep your production lines flowing smoothly. Ready to revolutionize your manufacturing process? Talk to us today, and discover how our SOFTBOT Platform can sweeten your operations. Let’s turn potential meltdowns into opportunities for growth and success.